Automation key to relieving pressure on nurses and supporting their retention in NHS
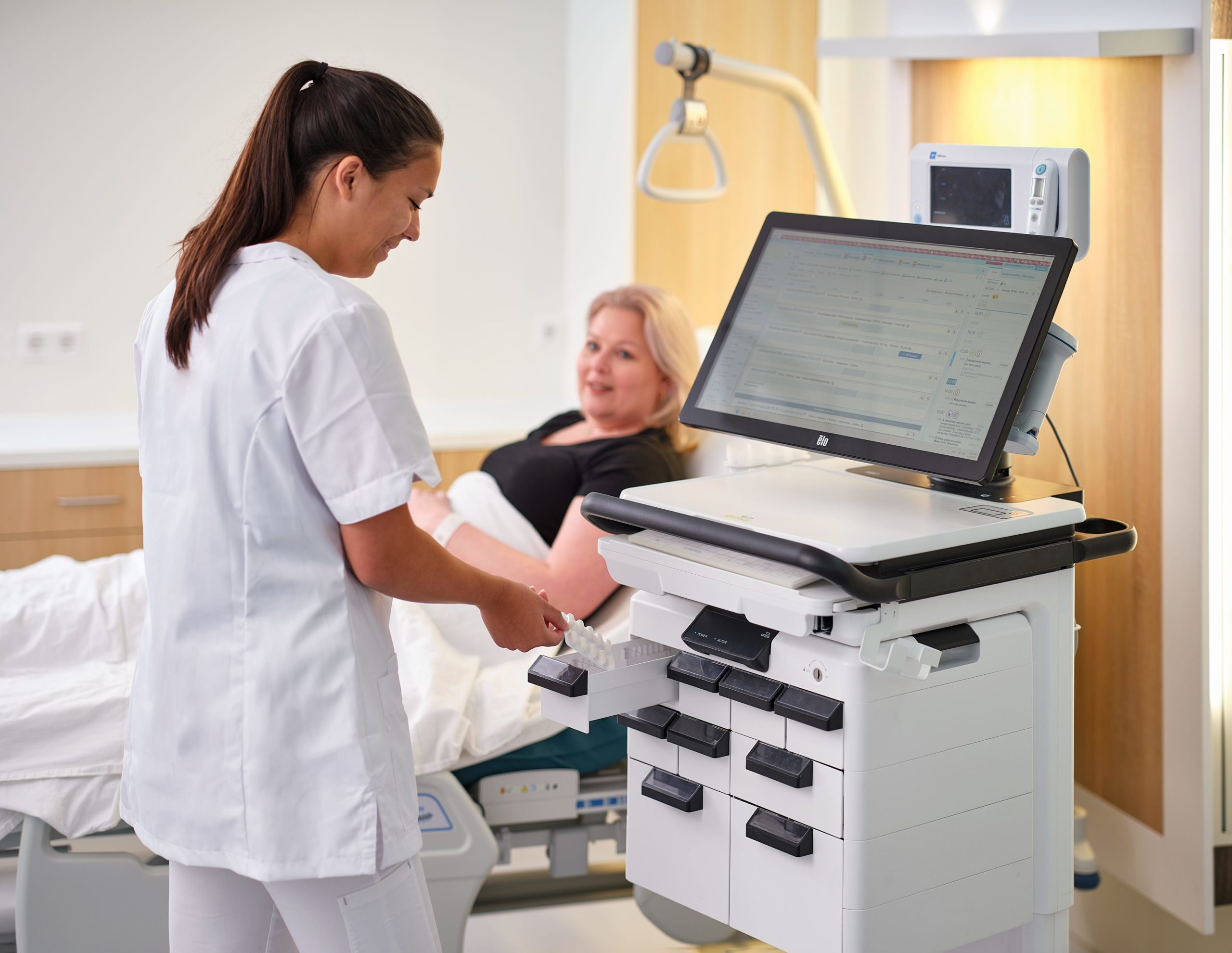
Every year in the UK, an estimated 273 million medication errors cost the healthcare system a staggering £98 million. When we look at the ‘typical’ NHS patient medication round, it’s easy to see why – it’s often loaded with inefficient processes which can create error, delay and a lack of transparency at the point of medication administration.
Those on the ‘frontline’, and who therefore carry the greatest burden from these challenges, are nurses. It is little wonder that nurse recruitment and retention is at an all-time low, with recent figures suggesting there are currently 47,000 unfulfilled nursing vacancies across the NHS.
The pressure on nurses is at an all-time high, including the management of increasingly complex medication needs – and this is set against a backdrop of record levels of bed occupancy and patient workloads in the NHS. Never has there been a greater need to harness technology to drive efficiencies and patient safety.
In my role as Senior Commercial Director of Omnicell’s UK and Ireland hospital division, I have witnessed the transformative effects automation can have on the workload of nurses, and strongly believe it holds the key to leaner and safer workflows in both ward and theatre environments. When done correctly, automation can free up nurses’ time spent on manual processes, reduce drug errors, and also save the NHS money.
A great example of automation in action is at Chesterfield Royal Hospital. The hospital is no stranger to automation, having embarked on this journey nearly 10 years ago with the installation of a range of Omnicell’s automated dispensing cabinets (ADCs). However, recently they became the first UK hospital to incorporate the AMiS-PRO Smart Cart onto one of their in-patient respiratory wards, with the key aim of trying to make their nursing team’s workflow smarter, faster and safer.
The Smart Cart harnesses intelligent technology to combine the functionality of a medication trolley with a computer on wheels, and dedicated locking medication bins. In its simplest terms, it enables nurses to make one trip away from the ward for each medication round, rather than one trip away from the ward for every patient, as is the case across most NHS Trusts today. It is also unique in giving complete oversight of what has been administered to who and when.
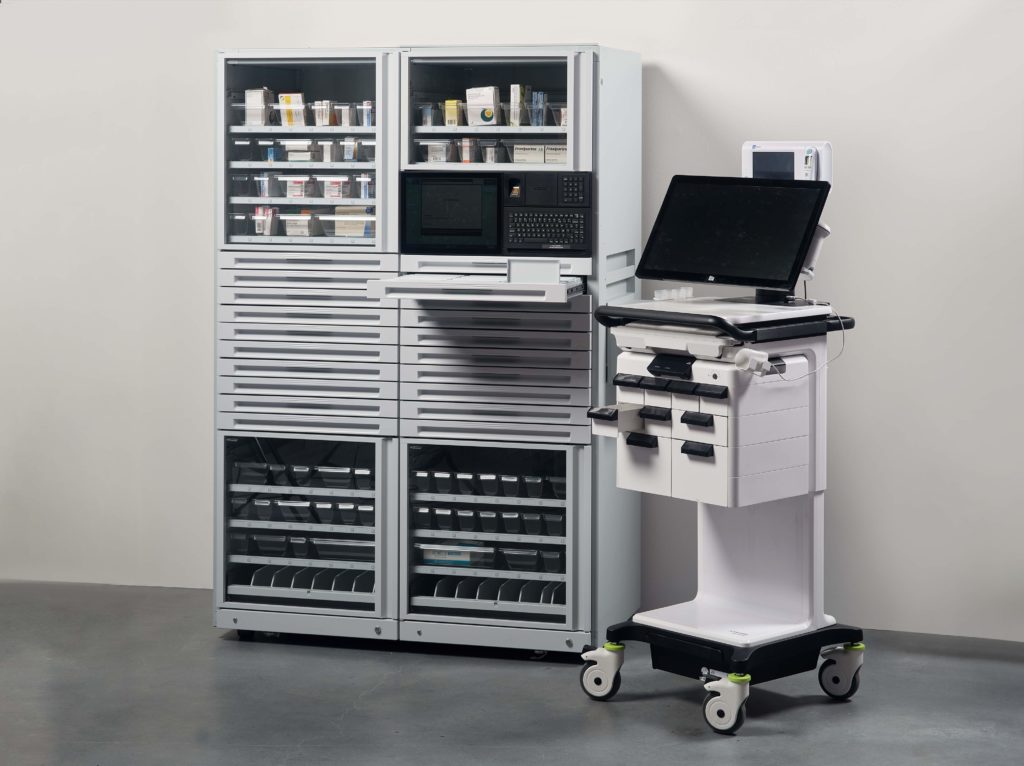
Andrew Hardy, Deputy Chief Pharmacist at Chesterfield Royal Hospital, was experiencing the common issues detailed above among his nursing team. So, to help gain a clearer picture where drug rounds were concerned, Andrew initiated a dedicated two-week audit on medicine administration rounds on its wards. This was in order to better understand the timings of each drug round, in addition to measuring the increasing complexities of medicine regimens.
The results made for interesting reading – the average time taken for each drug round, performed by a total of four nurses, was 47 minutes. 80 per cent of drug rounds had at least one interruption and 50 per cent had at least one medication missing. These findings, together with significant frustration among the team regarding consistency and the amount of waste produced from ‘one-stop’ dispensing, prompted Andrew to introduce the Smart Cart technology.
Andrew was also aware that to deliver the full benefits of automation, a ‘closed-loop’ model was needed. Their existing model – which incorporated a mix of both ADC cabinets and patient bedside lockers – was not enabling the technology to deliver to its full potential. Andrew had the key goal of ensuring 99.9 per cent of medications on their drug round wards were distributed from the ADCs, integrated with the AMiS-PRO Smart Cart, and with the EPMA system.
The initial results speak for themselves. Over a period of three months, on just one ward, there was a significant reduction (28 per cent) in missed doses – down from 480 per month to 250. There was a time saving of 30 minutes per drug round, equating to £2,000 in staff time savings, totalling an estimated £16,000 in savings per ward. In terms of dispensed items, they were able to decrease restock values by 20 per cent and achieve savings equivalent to £1,000 per ward, per month. Crucially, nurses were able to spend more quality time with the patient at the bedside.
We know from experience that getting a team to fully understand and support the need for technology adoption is key. Existing workflows have often been in place for many years, and a complete change of mindset is often required. Collaborative working across the board is therefore vital to ensure its success. Andrew’s experience echoed this – his entire team was involved with the adoption of the Smart Cart. For example, nurses were empowered to organise the drug round themselves, and support from the IT team helped establish the technology within the Trust as a whole.
Of course, with any form of technology introduction, testing and refining along the way is often required, and indeed recommended. Issues may crop up, aspects may need fine-tuning, and that is why a strong, collaborative partnership between the provider and Trust is also key.
Moving forward, Andrew plans to introduce the technology in the hospital’s in-patient diabetes ward, to ascertain how it works among their nursing teams and to see if they can achieve similar time and financial savings, whilst driving patient safety and transparency in its medication administration.
Further north, The Sandwell and West Birmingham NHS Trust is also on a mission to deliver a closed-loop workflow, with the installation of 80 of the AMiS PRO Smart Carts, with 60 Omnicell automated dispensing cabinets, and interoperability with Cerner. This is a truly ground breaking project and will define the way medicines are managed.
How the Amis Pro Smart Cart works, step-by-step: – The nurse views each patient’s electronic patient record (EPR) at the bedside, and then sends medication orders directly to an automated dispensing cabinet (ADC), eradicating the need for checking against printed medication lists and handwritten patient notes, thereby eliminating potential errors. – Once the nurse completes all patient medication orders on the round, all medications are collected from the ADC and placed within secured individual patient bins on the Smart Cart before being delivered to each patient, eliminating medication mixing errors that can occur using more traditional medication trolleys. – Finally, through integration with NHS Electronic Patient Record (EPR) and Electronic Medication Administration Record (eMAR) systems, all doses administered can be recorded, resulting in closed loop recording of medications, giving full transparency and recording at point of care of what medication was administered, when and by who. |
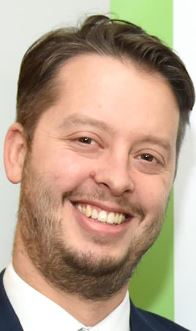
Edward Platt is Senior Commercial Director of Omnicell’s UK & Ireland hospital division, in addition to its UK community pharmacy division.
To find out more about how the AMiS-PRO Smart Cart could support your hospital, please visit: Omnicell.co.uk or email: Sales-aa@Omnicell.com